
Dirty condenser coils – The condenser will need to be cleaned.Remote or panel limiting in effect – This is a normal response when either the remote or panel limiting is in effect.High ambient temperature – This is a normal response from the controller when the ambient temperature is high.This is usually caused by different factors when the high-motor current anticipatory control activates current limiting. Inoperable fans – Check for an obstruction or damage.High ambient temperature – This can occur occasionally during normal operation.Broken discharge transducer – An authorized technician will need to check and repair.System Fault: Discharge Pressure Limiting Inoperable/broken feed or drain valve – Have the feed and drain valve checked for an authorized technician.Incorrect reading on transducer – The transducer could be broken.For low charge, an authorized technician check and remedy the subcooling. Low flow or charge – There could be low flow or charge in the unit.High superheat – An authorized technician will have to measure superheat to determine the cause.Dirty coils – An authorized technician will need to clean the coils.Condenser fans broken or running backwards – Have the fans checked, cleaned and repaired by an authorized technician.Broken discharge temperature sensor – Contact an authorized technician to check and repair the sensor.This system fault occurs when there is high temperature input from one of the sensors. Overcharged system – An authorized technician will need to remove charge and check the subcooling.Fans aren’t operating – If the unit’s fans aren’t operating, have the fan’s rotation, fuses and motor blades checked and remedied by an authorized technician.Damaged or dirty coils – Contact an authorized technician to clean coils, comb fins and make any necessary repairs.
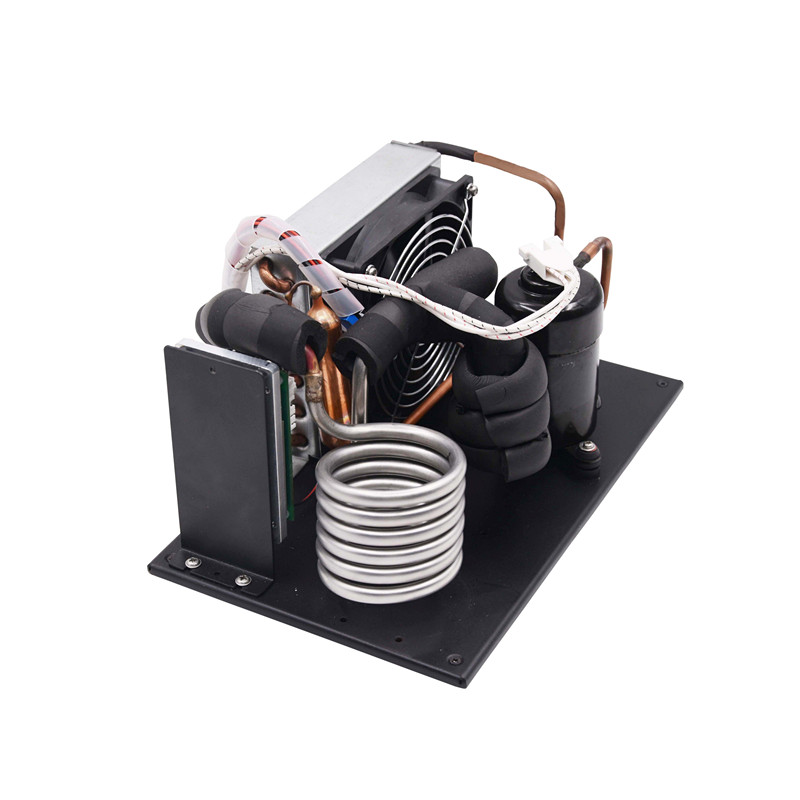
Dirty coils – Have the coils cleaned by an authorized technician.Condenser fans broken or running backwards – Have the fans checked, cleaned and repaired by an authorized technician.Broken oil temperature sensor – An authorize technician will need to verify if the reading is reasonable.Have an authorized technician check and repair the problem. If this fault appears, this means the system fuse has blown. Contact an authorized technician to check and repair any issues. Broken chilled water sensor – There could intermittent operation with the sensor or shorts in the wiring.Leaving chilled liquid temperature drops faster than unit can unload – There could be restricted flow or rapid flow changes, or the flow is below minimum for the unit.If the reading isn’t comparable, the sensor will need to be replaced.Ĭhiller Fault: Low Leaving Chilled Liquid

A tech will compare the temperature reading on the display to a thermometer reading at the sensor. Broken ambient sensor – Have an authorized technician check if the ambient sensor is broken.Ambient temperature too high – The ambient temperature could be above the maximum operating temperature.If the reading isn’t comparable, the sensor will need to be replaced.
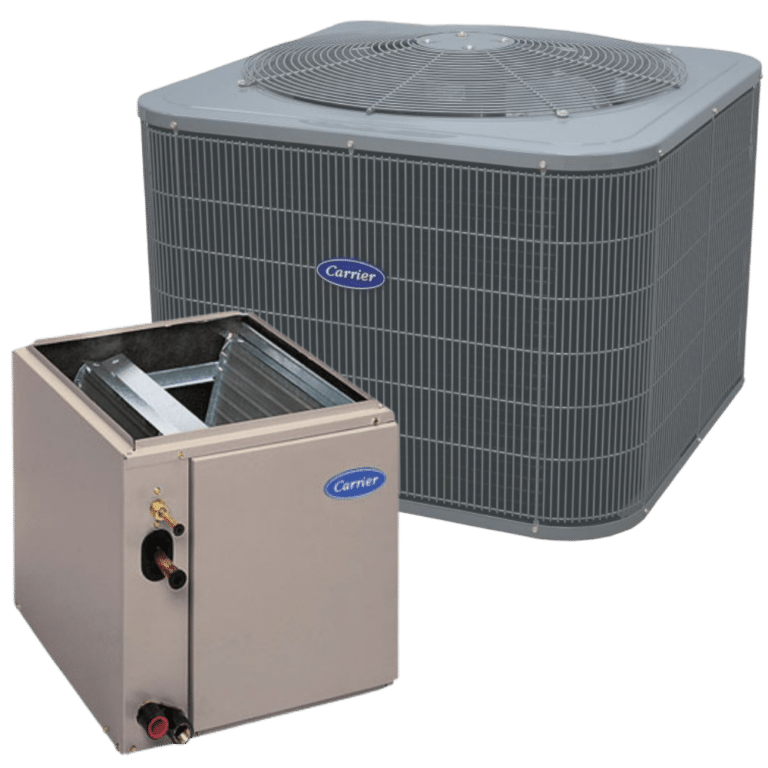
